Researchers develop concrete using local materials
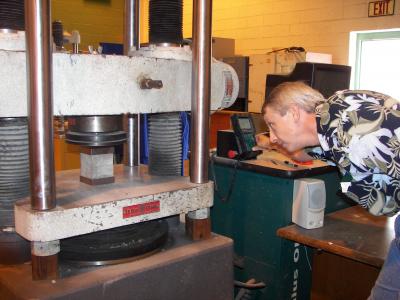
Because of their work and determination, New Mexico builders may soon be able to purchase high-strength concrete made from local materials, at half the cost they would currently pay for imported UHPC.
The team is now in the process of obtaining a patent for their product.
Research for the project originated with former NMSU student Srinivas Allena, who, in 2007 was working on his Ph.D.
"It was a very basic idea," he said. "My main determination was not to use any expensive, imported materials, because that drives up the cost of the final product."
Allena, who is now an assistant professor at Washington State University Tri-Cities, experimented with materials available in New Mexico and produced UHPC after rigorous optimization of mixture proportions. He tested the concrete's compressive and flexural strengths after 7, 14 and 28 days, and found his mixture comparable to commercially available pre-packaged UHPC.
"(Allena worked on) mixture proportions to produce concrete with local New Mexico materials that would yield strengths of 20,000 pounds per square inch (psi)," said Craig Newtson, NMSU civil engineering professor. "That kind of strength is ridiculously high and can be beneficial for things like for blast resistance (more immune to cracks and repairs)."
Because of those qualities, research soon began to move in the direction of bridge applications.
"UHPC is more expensive than traditional concrete,"Newtson said. "So we found that in order for the material to pay for itself, it would have to outlast traditional concrete."
After Allena's graduation, Newtson, along with fellow civil engineering professors Brad Weldon and David Jáuregui, submitted a proposal and received funding from the New Mexico Department of Transportation to continue Allena's research.
"The proposal was for a feasibility study to test whether the material could be used in bridge girder applications - specifically, pre-stressed concrete, which refers to a specific construction method," explained Newtson. "The steel is laid out - in this case, strands of steel - and there are large bulkheads at the end of the forms. The strands are pulled, prior to pouring in the concrete.
"When the concrete hardens, the strands are released, and they pull the bottom of the beams into compression, so the beams hunch up. When loads (of pressure) are applied, the beams come down to nearly flat."
Newtson added that pouring concrete over regular bars is cheaper, but requires more repair work in the long run, due to cracks.
The team, he said, hoped to examine two factors in their studies: bridge designs and economic analysis.
While Newtson developed the materials, Jáuregui and Weldon got to work analyzing structural behavior and bridge designs.
"We focused more on structural components and laboratory and field testing," said Jauregui, director of the NMSU Bridge Inspection Program. "Ultimately, we hope to see UHPC used in the field. We're getting ready to start phase three of the research, full-scale lab evaluation of UHPC beams."
Jáuregui said the current strength of concrete being used throughout the state is approximately 10,000 psi - half the strength of UHPC.
Ductal concrete, he added, is commercial UHPC developed in France and is shipped from Canada at 10 times the cost for normal concrete. Locally developed UHPC would sell at only five times the cost for normal concrete, he estimated. Because of proprietary regulations, there aren't many details on the ingredients of Ductal concrete, except that it's made from limestone and clay.
Newtson said UHPC's strength is comparable to low-grade steel.
"Steel ranges from 20,000 to 100,000 psi," he said. "(To produce steel), iron is separated from ore. It's pretty expensive."
"Concrete needs two things: strength and durablility," Allena said. "We succeeded in achieving strength comparable to commercially available UHPC products, now we need to improve the durability. My goal is to make this material available in two years, so the nation can save a lot of money.
"Aside from bridge girders, there are numerous applications for this concrete. The fact that we're using local materials to produce UHPC is most exciting. We've produced the UHPC in our own local facilities, with local materials in the cheapest way. That is actually a big leap towards sustainability."